How to disable "Air Suspension Fault" after Arnott conversion
#41
#43

Hi everyone,
I am half way through my suspension conversion however I am doing it a bit different. I am not using any aftermarket systems but instead using the S Types shocks. They essentially share the rest of the suspension and are of similar weight and so forth. I just finished the front and still have to do the back. However, not only do I get the fault message, I also get a put the car in Park and a chime goes off when ever the car is above 5 mph. I can deal with the messages but that chime has to go.
Can I unplug just the front suspension harnesses from the black box?
If anyone has an extra EBM from the Arnott, I will buy it from you.
I have an 08 vandan plas xj
Many thanks.
I am half way through my suspension conversion however I am doing it a bit different. I am not using any aftermarket systems but instead using the S Types shocks. They essentially share the rest of the suspension and are of similar weight and so forth. I just finished the front and still have to do the back. However, not only do I get the fault message, I also get a put the car in Park and a chime goes off when ever the car is above 5 mph. I can deal with the messages but that chime has to go.
Can I unplug just the front suspension harnesses from the black box?
If anyone has an extra EBM from the Arnott, I will buy it from you.
I have an 08 vandan plas xj
Many thanks.
Got the suspension failure code. In Texas this will not pass inspection. I checked the resistance of the shocks and it was 10-12 ohms. Tried 12 ohm resistors and it was intermittent codes. So tried 22 ohm and it was fine. In all four harness.
Later some burnt up. They were 5 watt. Put 12 watt 22 ohm power resistors and put another 80,000 on it. Transmission punked.
The Bilstein shocks may be different. I need to go measure the ones in the shed. What is inside the Arnott modules?
I notified Arnott about the resistors and they said it would not work. But it worked for several hard driving years with no codes.
The following users liked this post:
Don B (07-26-2016)
#44

It's been a while since I looked at the air suspension system but I do recall now that there is a connection between the Air Suspension Module and the Park Brake Module related to speed, since the park brake module gets a signal to disengage the park brake when moving, or to prevent it from being manually engaged while underway. This is the same signal that is used to set the CATS shocks firm when the vehicle is not moving, it's a message on the CANbus as I recall.
Frankly speaking, you can't expect to unplug half of a system and expect things to be working correctly. Get the rears swapped over to coils and disconnect the air suspension module like everyone else has. Then you should be down to just the one error message.
Frankly speaking, you can't expect to unplug half of a system and expect things to be working correctly. Get the rears swapped over to coils and disconnect the air suspension module like everyone else has. Then you should be down to just the one error message.
Last edited by Cambo; 07-26-2016 at 08:27 PM.
The following users liked this post:
Don B (07-26-2016)
#46

So you are driving the car with front coils and rear air? Things are acting up for that reason alone. Mine is so far converted to coils that I've remove all components associated with the air suspension clear down to some of the air lines. Only the harnesses themselves still exist. The module was a pain to remove because it required drilling out 4 rivets, but I was determined to take it out.
#48
#49

It will prompt that each time the battery is disconnected. You'll want to go through the window relearn procedure too so your auto up and down work again.
#50

The ASM is connected to the can network
It takes inputs from the IC and outputs codes
This in turn has the PBM connected via the SCP bus.
The PBM gets speed via the SCP to perform the disengage
Also the REM and PAM are linked to the SCP bus
The PIA used the SCP to output faults.
Reverse input is via the lamps
The REM supplies a switched speed signal to disable the PAM above 15kph to diable the chime
Fernando,
Ill also say having air on the rear and coils on the front is a bad idea
That said if you disconnect the ASM the rear suspension will end up deflated and damage the bags. With the ASM disabled it has no way of controlling them.
What you need to do is fool the ASM into thinking the front bags are fitted and are working.
First cap the air lines to the front bags.
You can do this with a push in fitting at the tube near the bags. A better way is to disconnect the tubes at the manifold in the boot and add a plug.
Next you need to fool the height sensor. You can do this with a resistor connected to the sensor plug or strap the sensor in the correct position.
Finally with the front shock plugs disconnected the ASM will sense this and put the rear shocks into hard mode. To fix this place a resistor over the plugs to fool the system that its connected. This is whats is done by Arnott air units. Just measure the resistance of the coil in your old air struts and match that
Cheers
34by151
It takes inputs from the IC and outputs codes
This in turn has the PBM connected via the SCP bus.
The PBM gets speed via the SCP to perform the disengage
Also the REM and PAM are linked to the SCP bus
The PIA used the SCP to output faults.
Reverse input is via the lamps
The REM supplies a switched speed signal to disable the PAM above 15kph to diable the chime
Fernando,
Ill also say having air on the rear and coils on the front is a bad idea
That said if you disconnect the ASM the rear suspension will end up deflated and damage the bags. With the ASM disabled it has no way of controlling them.
What you need to do is fool the ASM into thinking the front bags are fitted and are working.
First cap the air lines to the front bags.
You can do this with a push in fitting at the tube near the bags. A better way is to disconnect the tubes at the manifold in the boot and add a plug.
Next you need to fool the height sensor. You can do this with a resistor connected to the sensor plug or strap the sensor in the correct position.
Finally with the front shock plugs disconnected the ASM will sense this and put the rear shocks into hard mode. To fix this place a resistor over the plugs to fool the system that its connected. This is whats is done by Arnott air units. Just measure the resistance of the coil in your old air struts and match that
Cheers
34by151
Last edited by Don B; 07-29-2016 at 09:03 PM.
The following users liked this post:
Don B (07-28-2016)
#52
Join Date: Feb 2014
Location: Crossroads of America
Posts: 19,392
Received 12,739 Likes
on
6,380 Posts

34X151's solution should work. Somehow Arnott accomplishes the same result with their Electronic Bypass Module (EBM), with just four wires spliced to the harness near the (disconnected) ASM.
When I installed the Arnott coil conversion kit on a friend's XJ8, I attempted to measure the electrical properties of the EBM. Across each pair of the four wires, I measured for resistance, capacitance, inductance, and diode behavior. I could only get a meter reading across one pair of leads - a resistance in the 150 ohm range if I recall correctly. I couldn't get any meter value across the other pairs of leads. Possibly a limitation of my meter, or an indication that there are multiple semiconductors in the circuit and not simply passive components.
When I installed the Arnott coil conversion kit on a friend's XJ8, I attempted to measure the electrical properties of the EBM. Across each pair of the four wires, I measured for resistance, capacitance, inductance, and diode behavior. I could only get a meter reading across one pair of leads - a resistance in the 150 ohm range if I recall correctly. I couldn't get any meter value across the other pairs of leads. Possibly a limitation of my meter, or an indication that there are multiple semiconductors in the circuit and not simply passive components.
Last edited by Don B; 07-29-2016 at 09:02 PM.
#53

I can get the value if its needed but will be a a few days till I can do that.
PS the other way to do it is with a resistor wheel connected to the harness.
Just keep turning down the values till the error is lo longer triggered
After I get the value ill check using this method
Cheers
34by151
PS the other way to do it is with a resistor wheel connected to the harness.
Just keep turning down the values till the error is lo longer triggered
After I get the value ill check using this method
Cheers
34by151
#54

I can get the value if its needed but will be a a few days till I can do that.
PS the other way to do it is with a resistor wheel connected to the harness.
Just keep turning down the values till the error is lo longer triggered
After I get the value ill check using this method
Cheers
34by151
PS the other way to do it is with a resistor wheel connected to the harness.
Just keep turning down the values till the error is lo longer triggered
After I get the value ill check using this method
Cheers
34by151
#55

To put it simply you get a suspension faults under 2 conditions
1. Ride height out of limits
2. The air tank does not reach pressure in time (5mins I think)
How the ECU knows the ride height is a sensor on each wheel
If you look at page 05.3 in the electrical diagram you will see the 4 sensors marked as height sensor
The sensor has 3 wires
+5Volts, OVolts and output
All the sensor is is a pot or variable resistor
If you connect + power, ground to each end of a pot the 3rd pin give you a voltage between the two and relative to the the amount the pot is turned
IE all the way one way, output = the + power, all the way to the other end you get ground and it varies in between
So this is all the height sensor does give a voltage between o and +5 relative to the height of the wheel
If one of these signals is low the ecu signals the solenod to add air to the airbag raising the wheel. If the voltage is gigh it purges air. The goal being to achieve the value set in the SDD
If it cant do this you get a suspension height fault
So faking this will prevent the height fault as ithe ecu always thinks you have the correct height
For the Compressor waning, the ecu tries to keep a stable pressue in the tank. The tank is in the boot under the valve block.
The sensor is on the same page labels "Valve Block pressure sensor"
If you look at the page you will see its the same as the height sensor. The only difference is it varys the voltage based on the pressure in the tank
How the ECU reacts is to tun on the compressor when the pressure is low and turn it off when high. How the error is generated is with the pressure low it will run the compressor for 5 mins. If it does not get up to pressure in that time you get the error message.
So giving the ecu the correct voltage fools the ECU into thinking you have a pressurized tank
Hope that helps
If you read this post by cambo351 you will get the idea
The fisrt pic is the height sensor with the plug
Cheers
34by151
1. Ride height out of limits
2. The air tank does not reach pressure in time (5mins I think)
How the ECU knows the ride height is a sensor on each wheel
If you look at page 05.3 in the electrical diagram you will see the 4 sensors marked as height sensor
The sensor has 3 wires
+5Volts, OVolts and output
All the sensor is is a pot or variable resistor
If you connect + power, ground to each end of a pot the 3rd pin give you a voltage between the two and relative to the the amount the pot is turned
IE all the way one way, output = the + power, all the way to the other end you get ground and it varies in between
So this is all the height sensor does give a voltage between o and +5 relative to the height of the wheel
If one of these signals is low the ecu signals the solenod to add air to the airbag raising the wheel. If the voltage is gigh it purges air. The goal being to achieve the value set in the SDD
If it cant do this you get a suspension height fault
So faking this will prevent the height fault as ithe ecu always thinks you have the correct height
For the Compressor waning, the ecu tries to keep a stable pressue in the tank. The tank is in the boot under the valve block.
The sensor is on the same page labels "Valve Block pressure sensor"
If you look at the page you will see its the same as the height sensor. The only difference is it varys the voltage based on the pressure in the tank
How the ECU reacts is to tun on the compressor when the pressure is low and turn it off when high. How the error is generated is with the pressure low it will run the compressor for 5 mins. If it does not get up to pressure in that time you get the error message.
So giving the ecu the correct voltage fools the ECU into thinking you have a pressurized tank
Hope that helps
If you read this post by cambo351 you will get the idea
The fisrt pic is the height sensor with the plug
Cheers
34by151
1. Disconnect the battery
2. Push in a fitting at the tube near the two front bags (or disconnect the tubes at the manifold in the boot and add a plug)
3. Reconnect the two front height sensors, strap the sensors in the correct (medium) position, put and/or fix the sensors somewhere
4. Mount two resistors in the 150 ohm range (Don B's recall) instead of the front shock plugs or (safer option) wait a few days till 34by151 comes up with the exact measures of the resistors (coils)
5. Reconnect the battery
6. Do a test drive
7. Report your experience here
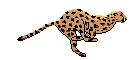
Last edited by LeoJagger; 07-29-2016 at 04:08 AM.
#56

No probs, get yourself a multi-meter.
Put it on resistance setting and measure the resistance of the pins on top of the shock.
If you can use an analog one it will give you a better reading
Id expect it to be in the range of 50-200 ohms
To confirm purchase a pair resistors as close to the value you measured
Any electronic shop will have plenty
Place the resistors into the plugs that normally go into the shocks
Reset the system (battery off) and clear any codes if present
Take it for a drive and confirm your OK
Cheers
34by151
Put it on resistance setting and measure the resistance of the pins on top of the shock.
If you can use an analog one it will give you a better reading
Id expect it to be in the range of 50-200 ohms
To confirm purchase a pair resistors as close to the value you measured
Any electronic shop will have plenty
Place the resistors into the plugs that normally go into the shocks
Reset the system (battery off) and clear any codes if present
Take it for a drive and confirm your OK
Cheers
34by151
Last edited by Don B; 07-29-2016 at 10:06 AM.
#57
Join Date: Feb 2014
Location: Crossroads of America
Posts: 19,392
Received 12,739 Likes
on
6,380 Posts

Note that the pins in the CATS electrical connector are very small in diameter and the test probe points on most meters are too large to fit down into the connector on the air spring/shock. You can use a couple of small paper clips, straightened, to insert into the connector, then measure across the paper clips.
Cheers,
Don
#58
Join Date: Feb 2014
Location: Crossroads of America
Posts: 19,392
Received 12,739 Likes
on
6,380 Posts

I've been pondering this. Securing the height sensor in a fixed position and leaving it connected to the harness should work without doubt.
But what I'm pondering is whether the circuit would respond properly to a simple resistor as a replacement for the sensor. According to the Dealer Training Manual, the ride height sensors are Hall Effect Transducers, not typical potentiometers. There are three wires for supply voltage, ground and feedback (like a potentiometer wired as a voltage divider), and the voltage returned to the ASM varies between 0.5V and 4.5V. Whether the circuit would respond properly to one resistor on the feedback wire or perhaps three resistors arranged in a "T" as a voltage divider, I do not know.
Have you actually done it, 34by151, and if so, what value of resistor(s) worked? I'm really curious now!
The Air Suspension and ECATS section of the Dealer Training Manual that I scanned can be downloaded here:
http://www.mediafire.com/download/7r...on_Section.pdf
Cheers,
Don
#60

As the position changes the voltage changes the output
So all you need a voltage divider. This can be done with a pair of resistors or a pot. The higher the value the better as its just the voltage feedback you need
I was experimenting prior to to building something with an Arduino.
I just had 3 (10meg/2W) pots connected to the ASM
What I was looking at was intercepting the 3 height sensors and outputting a different value (voltage) to the ASM.
The way the asm works is the voltages from the sensors are converted to a digital value. The ASM compares this to the stored value and adjusts the pressures of the shocks accordingly. The pressures are adjusted via the solenoids on the air manifold. There is some more stuff like the accelerometer, speed mode ect but this the basics
What the storeed value is is not the same for each car as no 2 cars will have the same adjustment on the sensors or weight balance. This is the reason for the adjustment in SDD.
If measured the volts prior to removing the front suspension you could use a simple voltage divider to foll the asm. As this in not know you will need to use a pot to work this out or in other words match the value SDD stored in the ASM. The other way around is to reprogram the ASM for the front using SDD. My suggestion would be to match the voltages of the rear sensors that way SDD will perform a level out and store the values you have set.
See this thread https://www.jaguarforums.com/forum/x...ur-x350-75369/
Cheers
34by151
Last edited by 34by151; 07-30-2016 at 01:32 AM.